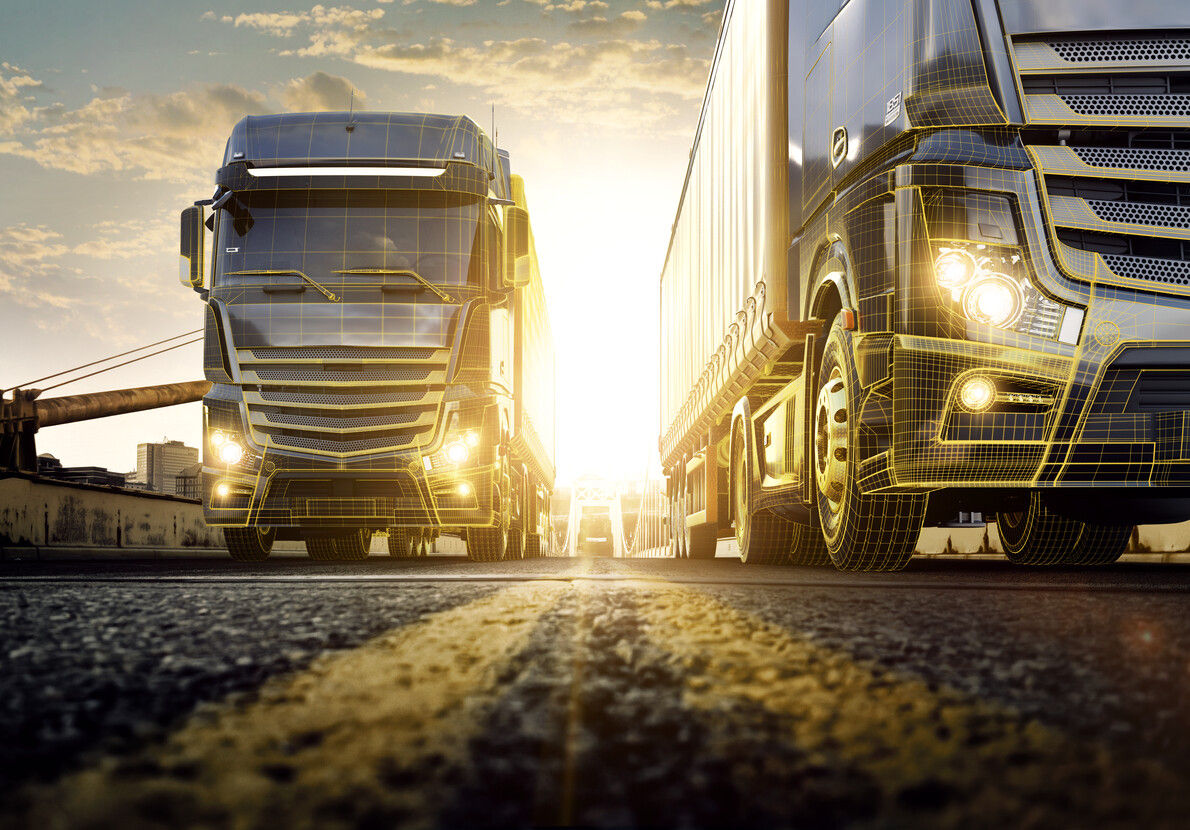
ContiLifeCycle
Choose a new life, instead of a new tyre.

#respectforretreads
What is a retread tyre?
Using our premium hot retreading service, you give new life to your worn truck tyre and realise the full economic performance of the tyre. During hot retreading, the process of applying the tread material is virtually identical to the production of a new tyre where the new rubber is extruded directly to the buffed casing. Afterwards the tread/casing assembly is cured in a vulcanisation mould with the required tread pattern. The pattern on the tread is formed during the vulcanisation process just as it is when a new tyre is made. To ensure a premium finish, every tyre is put through durability and safety tests in adherence to a standardised quality system.
Our ContiRe retreads are exclusively manufactured on Continental casings and provide a retread version of our existing Continental patterns, virtually identical to the new tyre. Our Bandvulc retread brand covers a wide range of specialist applications across its range.
Why choose retreads?
Source: The British Tyre Manufacturers' Association (BTMA)

Our ContiLifeCycle approach
We live in times of huge economic challenges. With increasing focus on safety, product compliance and sustainability today’s fleet operators require a holistic solution to ensure their products create the highest value, deliver maximum performance and meet their sustainability objectives. That’s why we’ve put together our LODC (Lowest Overall Driving Costs) philosophy and it’s designed to reduce tyre-related operating costs for our customers in the following ways…

As part of our Vision 2030 strategy programme, Continental has committed to an ambitious goal of becoming the most progressive tyre company regarding ecological and social responsibility by 2030. At the end of the decade, Continental aims to have more than 40% renewable and recycled materials in its tyres, with a drive to achieve 100% renewable and recycled materials by 2050 at the latest. The ContiLifeCycle programme is an important step on the road to fulfilling these core sustainability goals.
Retreading tyres for a more sustainable future.
Our retreading Plants, where the magic happens.
Our retreading Plants are located in Stöcken, Germany and in Ivybridge, UK, the former home of the Bandvulc Tyres facility. Continual investment into our operations ensures we remain at the forefront of retreading technology including sustainable practices, automation and research into rubber compound development.
Bandvulc’s heritage and expertise is key to aid our strategic plans into Continental’s innovation into the future of hot retreading, find out more about how our Ivybridge Plant has become the innovation hub for our ContiLifeCycle operation here.

Explore our mobility solutions further
-
2025/01/16Optimisation and AnalyticsRead more
-
2025/01/16Intelligent Tyre MonitoringRead more
-
2025/01/16Tyre Management SolutionsRead more
-
2024/10/24Tyre ServicesRead more
-
2025/01/16Premium Tyre ChoiceRead more
-
2024/11/21ContiConnectContiConnect fits your fleet – and your business. Improve your fleet’s performance with our tailored solutions for Digital Tire Management.Read more